5.1. Фізико-хімічні і технологічні властивості пресованих порошків
Таблетки - тверді лікарські засоби, які отримують шляхом технологічної обробки і пресування лікарських і допоміжних речовин, призначені для внутрішнього, зовнішнього, сублінгвального, імплантацій- ного або парентерального застосування.
За способом виробництва таблетки поділяють на два класи: пресовані, які отримують шляхом пресування лікарських речовин, і тритураційні, або формовані таблетки, що отримуються формуванням маси. Останні складають 1-2 % виробництва таблеткових лікарських форм.
Таблетки класифікують також за конструктивною ознакою і складом: прості (однокомпонентні) і складні (багатокомпонентні). За структурою: каркасні, одношарові і багатошарові, з покриттям (дражоване, плівкове і пресоване сухе) або без нього.
Таблетки для внутрішнього застосування поділяються згідно ДФУ:
- таблетки без оболонки;
- таблетки, покриті оболонкою;
- таблетки шипучі;
- таблетки розчинні;
- таблетки дисперговані;
- таблетки кишковорозчинні;
- таблетки з модифікованим вивільненням;
- таблетки для ротової порожнини.
Таблетки, отримані пресуванням, мають різну геометричну форму, масу і розмір. Вітчизняна промисловість випускає в основному таблетки округлої форми з плоскою або двоопуклою поверхнею
Розміри таблеток у діаметрі коливаються від 4 до 25 мм. Таблетки діаметром понад 25 мм називають брикетами. Найбільш поширеними є таблетки діаметром від 4 до 12 мм. Таблетки діаметром більше 13 мм повинні призначатися для розжовування, розсмоктування або розчинення перед уживанням; з діаметром 9 мм і більше повинні мати риску (одну чи дві), що дозволяє поділити їх на дві або чотири частини і таким чином полегшувати дозування лікарської речовини.
Деякі таблетки мають на своїй поверхні назву препарату або фір- ми-виробника. Вони зазвичай наносяться у вигляді увігнутих відбитків, оскільки опуклі знаки на торці таблетки більше схильні до стирання і руйнування.
Діаметр таблеток визначається залежно від їх маси. Для цієї мети користуються спеціальною шкалою “маса-діаметр” (ГОСТ 64-072-8JJ “Засоби лікарські. Таблетки. Типи і розміри”).
Даний ГОСТ передбачає в основному випуск двох типів таблеток: плоскоциліндричних без фаски і з фаскою, двоопуклих без покриття і з покриттям (плівкових, напресованих і дражованих). Плоскоцилін- дричні таблетки випускаються 14 типорозмірів з діаметром у діапазоні 4- 20 мм; двоопуклі таблетки без покриття випускаються 10 типорозмірів від 4 до 13 мм, таблетки з покриттям від 5 до 10 мм. Висота плоско- циліндричних таблеток повинна бути в межах 30-40 % від діаметра.
Маса таблеток в основному складає 0,05-0,8 г, що визначається дозуванням лікарської речовини і кількістю допоміжних речовин, що входять до їх складу.
Виробництво таблеток починається з вивчення властивостей вихідних лікарських речовин, які багато в чому зумовлюють раціональний спосіб таблетування, вибір асортименту і кількості допоміжних речовин. Як вихідний матеріал застосовують сипкі речовини у вигляді порошкоподібних форм (розмір частинок до 0,2 мм) або гранульованих (розмір частинок від 0,1 до 3 мм), які мають наступні властивості:
- фізичні - щільність, форма, розмір і характер поверхні частинок, сили адгезії (злипання на поверхні) і когезії (злипання частинок усередині тіла), поверхнева активність, температура плавлення та ін.;
- хімічні - розчинність, реакційна здатність;
- технологічні-об’ємна щільність, ступінь ущільнення, сипкість, вологість, фракційний склад, дисперсність, здатність спресовуватися та ін.;
- структурно-механічні — пластичність, міцність, пружність, в’язкість кристалічної решітки та ін.
Ці властивості часто підрозділяють на дві великі групи: фізико- хімічні і технологічні.
Порошкоподібні речовини складаються з полідисперсних систем, що мають різні форми і розміри кристалічних частинок (аморфна структура при виробництві таблеток зустрічається рідше). Форма і розмір частинок порошків залежать: у кристалічних речовин (хімі- ко-фармацевтичні препарати) - від структури кристалічної решітки та умов росту частинок у процесі кристалізації, у подрібнених рослинних матеріалів - від анатомо-морфологічних особливостей подрібнених органів рослин і типу подрібнюючої машини.
Частинки з подовженою і пластинчастою формою відносяться до анізодіаметричних (несиметричних, різноосних), а рівноосні - до ізо- діаметричних (симетричних) форм частинок порошків.
Відомо, що тільки речовини, які належать до кубічної системи, пресуються в таблетки безпосередньо, тобто прямим пресуванням, без грануляції і допоміжних речовин (натрію хлорид, калію бромід).
Зазвичай порошки, що мають частки у формі паличок, характеризуються дрібнодисперсністю, хорошою ущільнюваністю і достатньою пористістю (анальгін, норсульфазол, акрихін та ін.).
Порошки з рівновісною формою частинок - крупнодисперсні, з малим ступенем ущільнення, малою пористістю (лактоза, гексамети- лентетрамін, фенілсаліцилат). Чим складніша поверхня частинок порошку, тим більше зчеплення між ними і менша сипкість, і навпаки.
Фізичні властивості порошків визначаються питомою і контактною поверхнею та істинною щільністю.
Питома поверхня - сумарна поверхня, яку займає порошкоподібна речовина, а контактна поверхня - поверхня, яка утворюється при зіткненні між собою частинок порошку. Питома поверхня визначається методом повітропроникності на приладі - поверхнемірі. Питома поверхня перебуває у прямій залежності від ступеня дисперсності порошків і може варіювати в широких межах. Питома поверхня допомагає в процесі грануляції визначити розрахунковим шляхом кількість зволожувача — розчину зв’язуючої речовини.
Істинна щільність порошку визначається відношенням маси препарату до його об’єму, при нульовій пористості порошку.
За коефіцієнтом контактного тертя (/) опосередковано судять про абразившсть таблетованих мас. Чим більше його значення, тим стійкішим до зношування повинен бути прес-інструмент таблеткових машин. Найбільшу абразивність (/=0,2-0,4) мають неорганічні солі, крупно- кристалічні органічні речовини, рослинні порошки. Найменший коефіцієнт тертя (/< 0,2) у речовин з низькою температурою плавлення, з довгим вуглецевим ланцюгом, у гранульованих мас із змащуючими речовинами.
Для таблетування важливе значення мають такі хімічні властивості: наявність кристалізаційної води, розчинність, змочуваність і гігроскопічність. Якщо пружність пари в повітрі більша, ніж їх пружність на поверхні твердих частинок, то порошкоподібна маса, підготовлена до таблетування, починає поглинати пари води з повітря і розпливатися в поглиненій воді (гігроскопічність). На цьому основані умови зберігання і підготовки до таблетування таких препаратів. Молекули води кристалізаційної визначають механічні (міцнісні, пластичні) і термічні (відношення до температури повітряного середовища) властивості кристала і істотно впливають на поведінку кристала під тиском. Явище “цементації” також тісно пов’язане з наявністю кристалізаційної води в таблетованих препаратах.
Технологічні характеристики таблетованих мас перебувають у тісному взаємозв’язку з фізико-хімічними властивостями порошкоподібних лікарських речовин.
Порошки неоднорідні за розмірами частинок. Частинки порошку, що мають однакові розміри, складають фракцію. Співвідношення маси фракцій у відсотках називається фракційним, або у разі гранул — гранулометричним складом. Фракційний склад впливає на такі технологічні властивості порошків, як сипкість, здатність до спресовування, а також на міцність і середню масу таблеток, а, отже, на ритмічну роботу таблеткових машин, стабільність маси отримуваних таблеток, точність дозування лікарської речовини, якісні характеристики таблеток (товарний вигляд, здатність до розпадання, міцність та ін.).
Негранульовані порошки характеризуються поліфракційним складом і складною формою.
Більшість фармацевтичних препаратів, що підлягають таблетуванню, містять дрібну фракцію (менше 0,2 мм) у переважній кількості і тому мають погану сипкість. Вони погано дозуються за об’ємом на таблеткових машинах, таблетки виходять неоднорідними за масою і міцністю.
Дуже важливе визначення таких об’ємних показників порошків, як насипна і відносна щільність і пористість.
Насипна (об’ємна) щільність — це маса одиниці об’єму вільно насипаного порошку, яка залежить від щільності речовини, форми і розміру частинок, їх укладання. Лікарські порошки, як правило, легкі і сипкі, погрішність вимірювання їх насипної маси вища, ніж у важчих сипких матеріалів. Дозування таблеткових мас (порошків або гранул) у таблеткових машинах здійснюється за об’ємом, тому важливо знати насипну масу, від якої залежить вибір прес-інструмента, тобто діаметра матриці і пуансонів.
Відносна щільність — відношення об’ємної щільності до істинної.
Пористість - об’єм вільного простору (пор, порожнеч) між частинками порошку. У вільно насипаній масі порошкоподібних лікарських речовин частинки стикаються між собою тільки окремими ділянками своєї поверхні. Порожнечі (пори) у порошках можуть займати 50-80 % об’єму. Пористість порошкоподібної маси залежить від розміру частинок і їх форми. Чим менша щільність укладання, тим більша пористість маси і тим більший її об’єм, що вимагає більшого об’єму матриці. Від усіх цих об’ємних характеристик залежить здатність порошку до ущільнення під тиском. Чим менша щільність і більша пористість, тим більший ступінь стиснення порошку.
При таблетуванні порошкоподібних мас визначальними технологічними властивостями також є сипкість, ковзання і здатність до спресовування, шо дозволяє легко виштовхувати таблетку з матриці.
Сипкість характеризує здатність матеріалу висипатися з місткості (лійки) під силою власної ваги. Сипкість порошків є комплексною характеристикою, яка визначається дисперсністю і формою частинок, вологістю мас, гранулометричним складом, коефіцієнтом міжчастко- вого і зовнішнього тертя, насипною щільністю Ця технологічна характеристика може бути використана при виборі технології таблетування. Порошкоподібні суміші, що містять 80-100 % дрібної фракції (розмір частинок менше 0,2 мм), погано дозуються тому необхідно проводити направлене укрупнення частинок таких мас, тобто гранулювання. Якщо дрібної фракції міститься до 15 %, можливе використання методу прямого пресування.
Найчастіше сипкість визначають за швидкістю висипання певної кількості матеріалу (30-100 г) з металевої або скляної лійки із строго заданими геометричними параметрами і за кутом природного відкосу Визначення текучості сипких матеріалів за швидкістю витікання з лійки вимагає певного співвідношення між діаметром стебла лійки і розмірами частинок. Текучість може бути точно визначена при мінімальному впливі зависання порошку в тих випадках, коли співвідношення діаметра стебла лійки до максимального розміру частинок достатньо велике (більше 10-15).
Непрямою характеристикою сипкості є кут природного відкосу. При висипанні порошкоподібного матеріалу з лійки на горизонтальну площину він розсипається, набираючи вигляду конусоподібної гірки. Кут між твірною і основою цієї гірки і називається кутом природного відкосу.
Кут природного відкосу змінюється в широких межах від 25-35° для добре сипких і до 60-70° для менш сипких матеріалів. Звідси, чим менший кут, тим вища сипкість. Здатність порошку до спресовування - здатність його частинок під тиском пресування приймати і зберігати певну форму і розмір. Іншими словами, вона показує здатність частинок речовини при тиску під впливом різних сил до взаємного притягування і зчеплення з утворенням міцної структури.
Знання цієї величини дозволяє прогнозувати типорозміри таблеток (підбирати відповідний гірес-інструмент), правильно вибирати величину тиску пресування для отримання таблеток і підбирати оптимальний склад таблеток (допоміжні речовини) та їх технологію.
Безпосередніх методів визначення пресованості немає. Непрямою пробою на здатність до спресовування є визначення міцності модельної таблетки. Чим вища міцність таблетки, тим краща здатність до спресовування і формування таблеткових мас
За наслідками визначення пресованості таблеткових мас роблять висновок про технологію таблетування.
Сила виштовхування визначається з метою забезпечення виштовхуючого зусилля таблеток з матриць. Виникнення опору при виштовхуванні обумовлене тертям і зчепленням (адгезією) між бічною поверхнею таблетки і стінкою матриці.
Для визначення необхідних характеристик порошкоподібних речовин досліджують також пластичність, вологовміст і ряд інших показників.
Визначення форми, розміру і характеру поверхні порошку
Форму, розмір і характер поверхні частинок порошку визначають за допомогою мікроскопа, оснащеного мікрометричною сіткою або окуляр-мікрометром при збільшенні в 400 або 600 разів.
На поверхню предметного скла поміщають подрібнений порошок, потім поворотом на 180° його струшують при легкому постукуванні по склу. Визначають кристали по довжині і ширині (частинки анізодіаме- тричної форми) або по діаметру (частинки ізодіаметричної форми) за максимальними і мінімальними розмірами. Для отримання статистично достовірних результатів проводять не менше 50 вимірів для кожного порошку. Потім обчислюють середні показники.
Визначення вологовмісту
Дві наважки порошку масою 1-3 г, зважені з погрішністю ± 0,01г, помішують у заздалегідь висушені і зважені разом з кришками бюкси. Кожну наважку порошку сушать в сушильній шафі при температурі 100-105 °С до постійної маси.
Постійна маса вважається досягнутою, якщо різниця між двома подальшими зважуваннями після 30 хв. висушування і 30 хв. охолоджування в ексикаторі не перевищує 0,01 г.
Вологість сировини (X) у відсотках обчислюють за формулою:
|
За остаточний результат визначення беруть середнє арифметичне двох паралельних визначень, обчислених до десятих часток відсотка. Допустима розбіжність між результатами двох паралельних визначень не повинна перевищувати 0,5 %. Вологість порошків, що використовуються для виробництва таблеток, знаходиться в межах 3—5 %.
Визначення фракційного складу
100,0 г порошку зважують з погрішністю ±0,1 г, просівають через набір з чотирьох послідовно зібраних сит. Сита необхідно використовувати відповідно до статті ДФУ:
- грубі порошки (сито № 1400, діаметр 710 мкм);
- середнє подрібнення порошку (сито № 355, діаметр 224 мкм);
- дрібний порошок (сито № 180, діаметр 125 мкм);
- найдрібніші порошки (сито №125, діаметр 90 мкм).
Наважку порошку поміщають на верхнє сито і весь комплект струшують (вручну або на механізованому пристрої) протягом 5 хв. Потім сита знімають по черзі одне за одним. Просів і відсів матеріалу на ситах зважують. Вміст фракцій різної крупності виражають у відсотках від загальної маси. Фракцію, що пройшла через сито певного розміру, позначають знаком а що залишилася на даному ситі - знаком Наприклад, фракція, що пройшла через сито з діаметром отворів 224 мкм, але залишилася на ситі з діаметром отворів 125 мкм, повинна складати не більше 40 %, тоді записують: -224+ 125=40 %.
Визначення насипної щільності
Насипну (об’ємну) щільність порошку визначають на пристрої для вібраційного ущільнення порошків 545Р-АК-3 Маріупольського заводу технологічного устаткування (МЗТУ) (рис. 5.1).
Пристрій складається з основи 1, на якій розміщено електродвигун 2 і редуктор 3. На валу редуктора змонтований маховик 4 з ексцентриком 5. У стояку 6 розміщений шток 7; на верхньому корпусі його закріплена втулка 8, на яку за допомогою прокладки 9 і гайки 10 встановлений вимірювальний скляний циліндр 11 місткістю 25 мл. Амплітуду коливань регулюють за допомогою гвинта 14 і контргайки 15 за шкалою 12. Частоту обертання мотора регулюють трансформатором, а число коливань вимірювального циліндра фіксують лічильником 13.
Рис. 5.1. Прилад для визначення насипної щільності порошків |
Зважують 5,0 г порошку з точністю до 0,001 г і засипають його у вимірювальний циліндр. Встановлюють амплітуду коливань (35- 40 мм) за допомогою регулювального гвинта (14) і після відмітки за шкалою (12) фіксують положення контргайкою (15). Частоту коливань встановлюють за допомогою трансформатора в межах 100-120 кол/хв. за лічильником. Далі включають прилад тумблером (16) і стежать за відміткою рівня порошку в циліндрі. Коли рівень порошку стає постійним (зазвичай до 10 хв.), прилад відключають.
Насипну щільність розраховують за формулою:
|
Визначення істинної щільності
Істинну щільність порошку визначають за допомогою волюметра (пікнометр, який використовують для визначення щільності порошкоподібних твердих речовин).
Перед визначенням досліджувану речовину подрібнюють до порошкоподібного стану і висушують в сушильній шафі протягом 1,5-2 годин при температурі 100-105 °С (можна використовувати порошок, що залишився після визначення вологовмісту)
Спочатку визначають за пікнометричним фармакопейним методом відносну щільність рідини, вибраної для порівняння. Як рідину використовують будь-яку рідину, що змочує, але не розчиняє порошок. У той же волюметр, заздалегідь промитий, висушений і зважений з точністю до 0,0002 г, насипають 1—2 г досліджуваного порошку, зважують і по різниці мас волюметра точно визначають наважку взятої речовини.
Потім наливають у волюметр невеликими порціями рідину, кожного разу ретельно перемішуючи вміст струшуванням. Коли волюметр буде заповнений на 2/3, його поміщають на 1—2 години на водяну баню, нагріту до 60-65 °С, для видалення з порошкоподібної речовини повітря (або 10 хв. волюметр витримують у вакуум-ексикаторі). Після того, як видалено повітря, волюметр охолоджують, доливають рідину до мітки і зважують.
Істинну щільність (р, г/см3) порошку визначають за формулою:
|
Визначення відносної щільності
Відносна щільність (т, %) розраховується як процентне відношення насипної (об’ємної) щільності до істинної щільності:
|
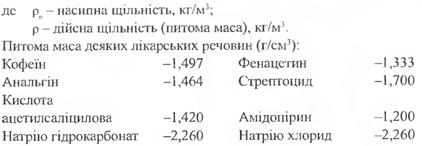
Визначення пористості
Пористість (П, %) визначається виходячи із значень насипної (об’ємної) щільності та істинної щільності:
|
Визначення сипкості
Визначення сипкості порошку проводять на вібропристрої для зняття характеристик сипких матеріалів ВП12А МЗТУ (рис. 5.2).
Вібропристрій складається з корпуса, всередині якого змонтовані всі функціональні вузли. У приладі передбачена вібрація конусної лійки шляхом жорсткого з’єднання її з електромагнітним пристроєм, що працює від мережі змінного струму. Наважку порошку масою 50,0 г, зважену з точністю до 0,01 г, засипають у лійку (1), заздалегідь знявши кришку (2). Включають пристрій тумблером (3) при закритій заслінці (4)
і одночасно включають електромагніт (5) і секундомір. Електромагніт притягує якір (6), стискаючи амортизатор (7). Із частотою 50 Гц вібрація від якоря передається лійці, яка зв’язана з якорем за допомогою тяги (8)
і шарніра (9). Після 20 с. утруски, необхідної для отримання стабільних результатів, відкривають заслінку (4) і спостерігають за витіканням порошку з лійки у приймальний стакан (10). Точність відліку часу закінчення до 0,2 с. Після закінчення витікання прилад відключають.
Рис. 5.2. Прилад моделі ВП-12А для зняття характеристик сипких матеріалів Сипкість розраховують по формулі: |
|
Непрямою характеристикою процесу сипучості є визначення ку га природного відкосу — кут між твірною конуса з сипкого матеріалу (11)
і горизонтальною плошиною (12). Дану характеристику визначають за допомогою того ж приладу.
Заздалегідь установлюють об’єм порошку, який повинен заповнити кільце (12), з утворенням гірки (11). Потім отриманий об’єм порошку засипають у лійку, включають вібропристрій. відкривають заслінку. Після закінчення порошку вимикають вібропристрій, прибирають надлишки порошку і підводять кутомір (13), визначаючи за шкалою кут природного відкосу.
Остаточні висновки за показниками сипкості і кута природного відкосу проводять виходячи з п’яти повторних вимірювань
Визначення здатності до спресовування
Для визначення здатності до спресовування (пресованості) матеріалу наважку порошку масою 0,3 або 0,5 г пресують у матриці з діаметром отворів 9 або 11 мм відповідно на гідравлічному пресі при гиску 120 МПа. Наважку порошку відважують на ручних терезах, поміщають у матрицю, що підтримується на нижньому пуансоні, і вставляють верхній пуансон. Всю прес-форму поміщують на середину плунжера гідравлічного преса і пресують до вказаного тиску, відміченого на манометрі.
Після запресовки таблетку виштовхують з матриці нижнім пуансоном на тому ж гідропресі.
Отриману таблетку зважують на торсійних терезах, висоту вимірюють мікрометром і коефіцієнт пресованості (К , г/мм) обчислюють за формулою:
де m - маса таблетки, г;
H - висота таблетки, мм.
Пресованість може бути оцінена по міцності таблетки на стиснення. Міцність визначають на приладах ХНІХФ1 або ТВТ фірми «Ервека»
і виражають у кілограмах або ньютонах.
Визначення сили виштовхування таблеток з матриць
Для визначення тиску виштовхування наважку порошку масою 0,3 або 0,5 г пресують у матриці з діаметром отворів 9 або 11 мм відповідно на гідравлічному пресі при тиску 120 МПа. Виштовхування запресованої таблетки проводять нижнім пуансоном При цьому на манометрі преса реєструється виштовхуюче зусилля.
Розрахунок виштовхуючого зусилля проводять по формулі:
Результати дослідження фізико-хімічних і технологічних властивостей порошків заносять у таблицю. |