3.3.5. Порошкова металургія
В електричних машинах і трансформаторах застосовують деталі, виготовлені методами порошкової металургії. До таких виробів належать: контакти регуляторів напруги трансформаторів; контактні кільця; колекторні пластини; пазові клини; постійні магніти та інші деталі обертових електричних машин.
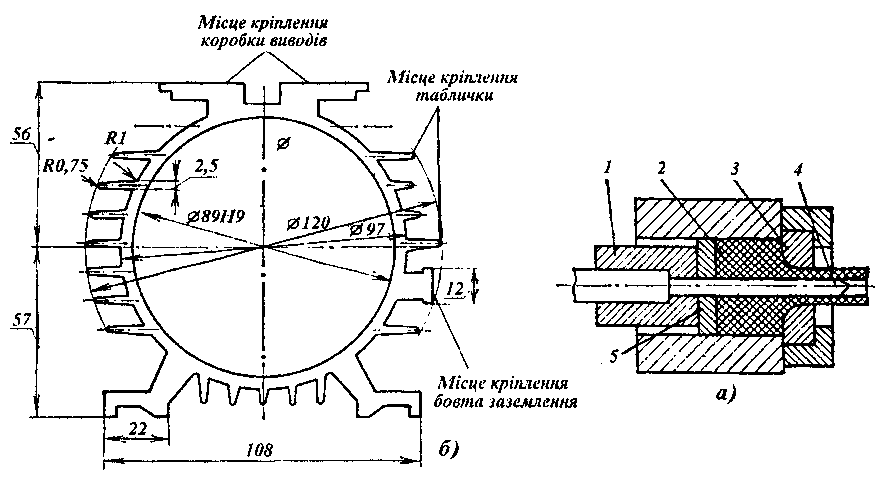
Рис. 3.16. Принцип гарячого пресування алюмінію' а - схема пресування; б - поперечний перетин профілю, який можна отримати пресуванням
Порошкова металургія - виготовлення деталей з металевих порошків та їх сумішей з неметалевими матеріалами без розплавлення основного компоненту'.
Механічні властивості виробів з чистих металевих порошків наближаються до властивостей литих матеріалів.
Технологічний процес виготовлення деталей складається з таких технологічних операцій: приготування шихти, дозування, пресування, спікання, термообробки, калібрування та обробки різанням.
Процес приготування шихти полягає в подрібненні порошків на кульових млинах, відпалюванні в захисному або відновлювальному середовищах та змішуванні порошків.
Шихту дозують за масою або за об’ємом і піддають пресуванню на гідравлічних або кривошипних пресах. Зусилля пресування 20 - 200 тс. Елементи прес-форм виготовляють з конструкційних хромонікелевих сталей за 7-Ю квапітетом точності з шорсткістю поверхонь Rа=1,25 / 0,32 мкм.
При конструюванні деталей, що виготовляються методами порошкової металургії, необхідно дотримуватися таких правил:
• деталі не повинні мати різей;
• деталі повинні мати плавні переходи від тонких перетинів до товстих;
• радіуси заокруглень повинні бути не менше 1 мм;
• висота деталі не може значно перевищувати її найменший розмір у плані, наприклад, при виготовлені циліндра, його висота повинна бути не більше трьох діаметрів.
Спікання виконується при температурі 0,65-0,75 від температури плавлення основного компоненту суміші. Витримка при цій температурі повинна бути 30-80 хв. Процес здійснюється у водневих або вакуумних пічках неперервної дії.
Після пресування і спікання деталі мають 11-13 квалітет точності розмірів. Для підвищення точності до 8-10 квалітету виконують калібрування, яке проводять при тиску до 10 000 кгс/см.
Після виконання всіх зазначених вище операцій деталі можна піддавати обробці різанням, здійснювати цементацію, наносити гальванопокриття.