3.5. Розкрійно-заготівельні роботи
При виготовленні конструкційних елементів електромеханічних перетворювачів, як вже було зазначено раніше, досить широко використовують листовий і сортовий прокати різного виду.
Під поняттям заготівельні роботи будемо розуміти ту частину технологічного процесу виготовлення деталей електромеханічних перетворювачів, яка полягає в підготовці листового і сортового прокату до штампувальних операцій або інших видів механічної обробки. При виконанні заготівельних робіт матеріалам, що надійшли з підприємств-виготівників, надають форми і розміри, які забезпечують мінімальну трудомісткість виготовлення деталей та їх максимальне використання.
Основна суть заготівельних робіт при підготовці листового прокату до штампувальних операцій полягає в поздовжньому та поперечному розрізуванні листів.
Поздовжнє розрізування рулонних матеріалів найбільш ефективно здійснюється за допомогою багатодискових ножиць, які дають змогу здійснювати різання неперервно. Конструкцію і принцип роботи таких ножиць пояснює рис. 3.18.
Економний розкрій сталі досягається за рахунок оптимального підбору ширини полос, на які розкроюється рулон. За такого розкрою з двох боків рулону обрізаються кромки по 7 - 10 мм. Це зумовлено тим, що налагодити внутрішнє поздовжнє розрізання точно паралельно до кромок неможливо, а, до того ж, кромки рулону бувають пошкодженими під час транспортування. Розкрій рулонних матеріалів значно простіший, ніж листових.
Залежно від товщини сталі і кількості полос, що нарізаються, розтинати рулон можна за принципом "привідного розрізу” (при товщині 0,3 мм і менше), і ’’тягнучого розрізу” (при товщині більше 0,3 мм).
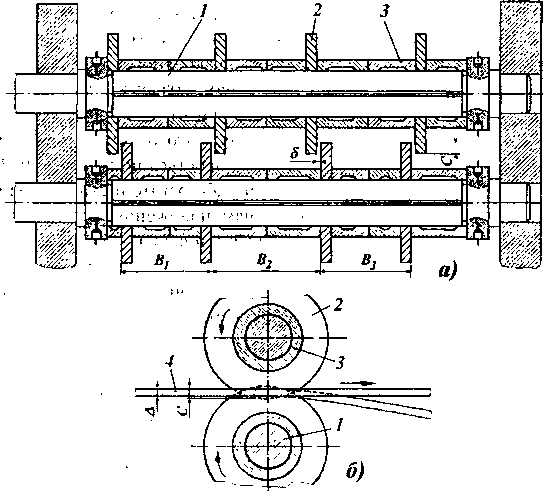
Рис. 3.18. Схема (а) і принцип дії (6) багатодискових ножиць для розрізування рулонного матеріалу на полоси завширшки В1, В2 і В3
1 - вал ножовий; 2 ~ ніж дисковий; 3 - втулка розпірна; 4 - матеріал, що піддається розрізуванню; 3 - боковий проміжок між ножами;
С - перекриття ножів; Л - товщина матеріалу
Метод "тягнучого розрізу” характеризується тим, що привід багатодискових ножиць відключається і полоса сталі протягується через ножові диски за рахунок намотувача. При цьому, швидкості різання і намотування стрічок на барабан однакові і не потребують спеціальної синхронізації їх руху. Якщо ножі не обертаються, то при різанні тонкого матеріалу або при невеликій кількості полос, розкрій виходить нерівний. У цьому випадку різання раціонально здійснювати за методом "привідного розрізу”, тобто коли багатодискові ножиці приводяться в рух^ від власного приводу. Швидкість різання залишається постійною, а швидкість обертання намотувача залежить від діаметра рулону, на який змотують полоси. Синхронізація швидкостей досягається завдяки установці спеціальних муфт обгону або використанню синхронізуючих електричних схем. Якість різання і точність геометрії розрізуваних полос залежить від конструкційних показників якості різальних дисків, якості їх заточування, налагоджування і правильного монтажу обладнання ліній. Швидкість різання на лініях поздовжнього різання -60-ь80 м/хв,а в ^ деяких випадках навіть - 120 м/хв.
Дискові ножиці використовують для виготовлення так званих ’’косих стрічок” - стрічок, ширина яких змінюється по їх довжині. Такі стрічки виготовляються на однодискових або багатодискових роликових ножицях з програмним керуванням положення дисків під час нарізання стрічок. ’’Косі стрічки" використовують, наприклад, при виготовленні витих просторових магнітопроводів трансформаторів
З метою економії сталі користуються фігурним розкроєм широких рулонів на окремі фасонні стрічки. Такі стрічки можна отримати за допомогою багатодискових ножиць з фігурними ножами (метод "скро-лайн”), ножиць з програмно керованими дисковими ножами або на пресах-автоматах з ножовими штампами (метод ”зіг-заг”).
Під час використання згаданих методів розкрою в фасонних стрічках пробивають технологічні отвори для фіксації їх на вловлювачах штампів під час подальшого автоматичного штампування. При виготовленні стрічки необхідно витримати високу точність повторювання кроку і між центрувальними отворами і точність їх розташування всередйні кожної фігури.
На рис. 3.19, а показано, як розділяють широкий рулон на окремі фасонні стрічки за методом ’’скролайн", а на рис. 3.19, б - подальше використання такої стрічки. На рис. 3.20 показано принцип реалізації методу "зіг-заг", який полягає в тому, що на першому етапі заготівельної операції компаундним штампом від рулону відокремлюють всі затемнені на рисунку елементи, а на другому - роблять розокремлення рулону на окремі стрічки 1, 2 і 3, що реалізується за допомогою ножових (розокремлювальних) штампів.
Поперечний розкрій листів, як правило, здійснюють гільйотинними ножицями. Для розрізування листів на задані розміри користуються ступінчастим упором, який встановлюється на столі ножиць. Недоліком гільйотинних ножиць є низька продуктивність. %
Різання товстого листового металу здійснюється методами кисневого (газового) чи плазмово-дугового різання. Ці методи забезпе-
чують можливість вирізання з листів деталей будь-якої конфігурації, скошувати кромки під зварювання, здійснювати розтинання профільних металів великої товщини.
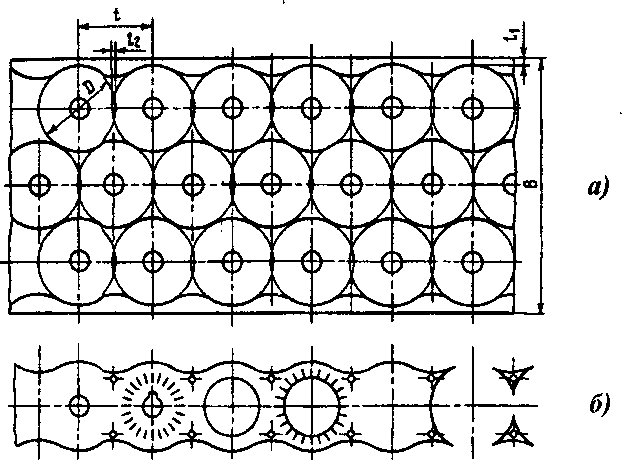
Рис. 3. і і Фасонний розкрій рулонної сталі за методом “скролайн'
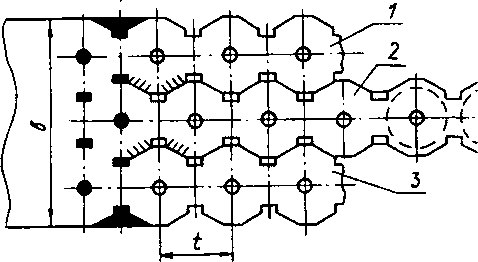
Рис. 320. Фасонний розкрій рулонної сталі за методом “зіг-заг '*
Різання виконують за картами розкрою, які забезпечують найбільш раціональне використання матеріалів. На рис. 3.21 показано, приклад розкрою листа сталі для виготовлення деталей великої електричної машини. Розкрій таких листів виконується на машинах з програмним керуванням.
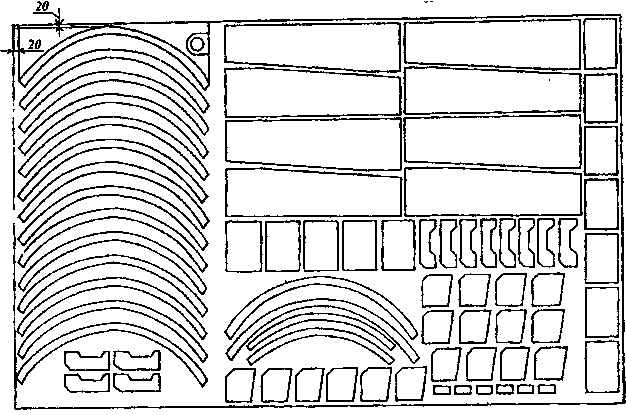
Рис. 3.21. Розкрій листового матеріалу при виготовленні деталей великої електричної машини
Газове різання металів базується на властивості інтенсивного горіння розпечених металів у промені чистого кисню. Для реалізації цього процесу використовують спеціальні ацетиленові, бензинові або плазмово-дугові різаки.
Плазмово-дугове різання порівняно з іншими видами розкрою, має суттєві переваги: швидкість різання в 3-5 разів більша на нижній кромці металу, практично не утворюється грат, теплові деформації значно менші, крім того, воно дуже ефективне при розтинанні алюмінію, мідних сплавів, корозійностійкої сталі, можна різати неелектро-провідні матеріали (кераміку, скло, бетон тощо).
Чистота і ширина розрізу залежить від способу різання. Машинне різання дає більш чисті кромки і меншу ширину розрізу, порівняно з ручною.
Стаціонарні машини для різання металів дають змогу забезпечити відтворення заданого контуру з точністю до 0,5 мм. При різанні металів завтовшки 5-15 мм ширина різу знаходиться в межах 2-2,5 мм, завтовшки 15- 30 мм - 2,5 - 3,0 мм, завтовшки 30 - 60 мм - 3,0 -3,5 мм.
Мірні заготовки з круглих і фасонних профілів при масовому та серійному виробництвах отримують рубанням прутків на пресах. При одиничному та дрібносерійному виробництвах такі заготовки одержують розрізуванням прутків фрезами чи абразивними кругами або з використанням механічних ножівок.