17.2.1. Виготовлення валів потужних електричних машин
Вали потужних електричних машин належать до найбільш навантажених деталей. Гїри роботі машини на вал діють значні навантаження від маси ротора, сил динамічної неврівноваженості та сил магнітного тяжіння. У зв’язку з цим висуваються високі вимоги до механічних характеристик матеріалів, з яких їх виготовляють, точності обробки та шорсткості поверхонь.
Залежно від конструкційного виконання машини вали поділяють на такі види:
•безфланцеві вали з двома підшипниковими шийками (рис. 17.14), які найбільше поширені в електричних машинах;
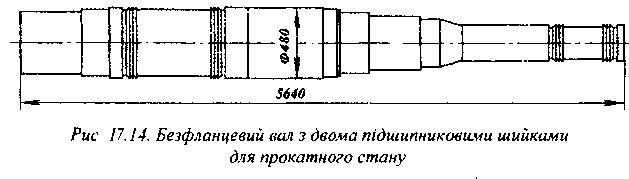
•фланцеві вали (рис. 17.15), які застосовують в одноопорних машинах;
•вали з приварними ребрами (рис. 17.16), які широко застосовують у машинах середніх потужностей;
• ребристі вали (рис. 17.17);
•вал-ротори (рис. 17.18), які використовують у неявнополюсних синхронних машинах, зокрема, в турбогенераторах.
Токарна обробка валів потужних машин поділяється на три етапи: чорнове обточування - обдирання, напівчистове обточування і чистову обробку - опоряджування. Обробка здійснюється на універсальних токарних верстатах.
Перед чорновим обточуванням виконують центрування однієї сторони заготовки. Положення центра знаходять за допомогою розг
мінування і кернять. Після цього на торці наносять контрольну кільцеву риску, 5а якою визначають рівномірність розташування припуску відносно знайденого центра. Обробляння центрових отворів виконують на горизонтально-свердлувальних верстатах; інструментом служать свердло і кутова зенківка.
Заготовку вала нецентрованим кінцем встановлюють у кулачках планшайби токарного верстата, а з іншого боку її підтискають центром задньої бабки. Пересуваючи кулачки, здійснюють виставку заготовки з найменшим биттям.
Після попереднього обдирання заготовки (зняття кірки) здійснюють поздовжнє розмічування місць розташування уступів вала. З цією метою на заготовку різцем наносять кільцеві риски.
Весь припуск на чорнову обробку прагнуть зняти за один установ з найменшою кількістю проходів. Після обточування на одній або двох ділянках вала шліфують базові пояски, які будуть використовуватися при подальшій обробці. З одного або з двох торців заготовки вирізають кільцеві зразки, необхідні для перевірки властивостей матеріалу. Всі ділянки вача повинні бути оброблені до шорсткості поверхні Rz=2,5-1,25 мкм, що необхідно для виконання ультразвукової дефектоскопії заготовки.
Після завершення чорнової обробки вал знімають з верстата і піддають ультразвуковій дефектоскопії Вали відповідальних машин та машин з луже важкими умовами експлуатації піддають природному або штучному старінню. В останньому випадку термічна обробка виконується заводом-поставником поковки.
Два останніх етапи токарної обробки, як правило, виконуються за один установ. Один кінець вала затискається в кулачках патрона, а для підтримування іншого кінця використовують люнети, кулачки яких спираються на пояски, оброблені при першому встановленні вала на верстат. Якщо базова поверхня вала (поясок для встановлення на люнет) не має правильної циліндричної форми, то за допомогою спеціального пристрою, встановленого на супорті токарного верстата, здійснюють шліфування пояска безпосередньо над кулачками люнету.
Вал встановлюють на люнети і виконують напівчистову обробку всіх ділянок вала і чистову обробку ділянок, призначених для встановлення остову ротора, колектора, вентилятора та інших деталей.
Чистове обточування кінців вала і підшипникових шийок виконується після складання ротора і намотування обмотки. Для кінцевої обробки підшипникових шийок застосовується метод чистової обробки пластичним деформуванням - накатування роликом.
При обробці валів з центральними отворами (вали гідрогенераторів (рис. 17.15) швидкохідних машин тощо) спочатку виконується чорнова обробка зовнішньої поверхні, як це було розглянуто вище, після чого здійснюється свердлування і чорнове розточування центрального отвору. Вал піддається повторній термічній обробці, здійснюється ультразвукова дефектоскопія і виконується чистове розточування отвору
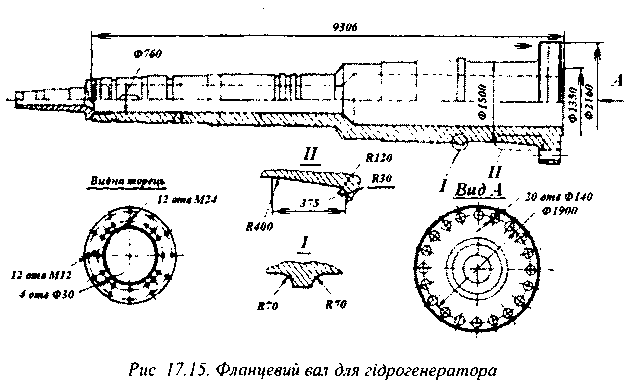
Вали з привареними ребрами (рис. 17.16) виготовляють з мало-вуглецевої сталі. Ребра 1, які приварюються до вала 2, вирізають з товстолистової сталі. Складання вала з привареними ребрами починається з розмічування, власне, вала, на якому наноситься поздовжня риска, паралельна його осі, і кільцева риска, за якою надалі будуть встановлюватися ребра 3 обох боків на вал встановлюються шаблони з прорізами для ребер, які закріплюються за допомогою стопорних гвинтів. Ребра 1, з привареними до них брусами 3, за шаблонами виставляються на валі і з обох боків прикріплюються до нього короткими
зварними швами. Між ребрами встановлюються технологічні розпорки, які за допомогою зварювання прикріплюються до них.
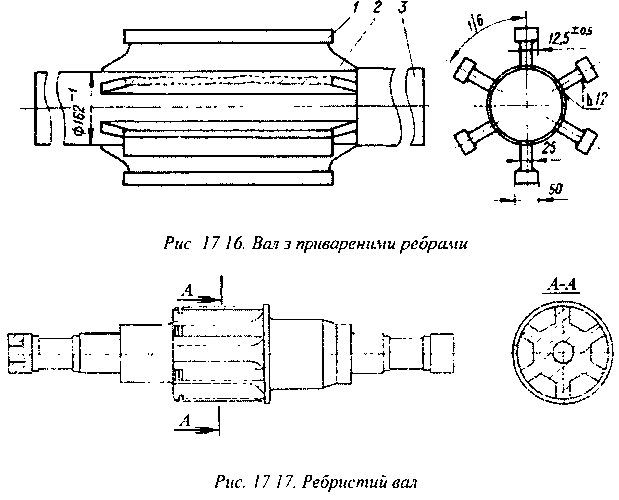
Перший прохід зварювального шва здійснюється з одного боку будь-якого ребра. Наступний шов накладається обов’язково на діаметрально протилежному ребрі, з того самого боку ребра, що і на першому. У такому ж порядку накладаються перші шви на всіх інших ребрах. Зварюють від середини ребра до його кінця. Після чого виконується по одному проходу зварювального шва на протилежних боках ребер. Послідовність накладання швів така ж, як і в попередньому випадку.
Кількість проходів залежить від розміру катету шва Так, наприклад, шов, показаний на рис. 17.16 (катет 12 мм), виконується за 6 проходів.
Вал з привареними ребрами піддається відпалюванню для зняття внутрішніх напружень. Подальша механічна обробка вала з привареними ребрами аналогічна до описаного вище.
Заготовки для ребристого вала (рис. 17.17) отримують методами кування з наступною механічною обробкою міжреберних порожнин Подальша обробка ребристого вала аналогічна описаній вище. Заготовки вал-роторів виготовляються з легованих сталей марок ОХНЗМ, ОХН4МАР, 35ХНЭМФАР та інших видів сталей високої якості Заготовки вал-роторів потужних турбогенераторів сягають граничних значень, за можливостями отримання відливок. Наприклад, ротор турбогенератора потужністю 800 МВт виготовляється з відливки масою 200 т, а турбогенератора 1200 МВт - 235т. Діаметр ротора двополюсного турбогенератора сягає 1120 мм, а довжина - понад 12 м.
Основні операції обробки циліндричних поверхонь вал-роторів аналогічні тим, що виконуються при виготовленні безфланцевих валів з двома підшипниковими шийками і фланцевих валів для гідрогенераторів.
Найбільш трудомісткою і відповідальною операцією під час механічної обробки вал-роторів є фрезерування пазів під обмотку і струмопроводи та вентиляційних пазів. Фрезерування виконується на спеціальних багатошпиндельних роторно-фрезерних верстатах.
На рис. 17.18 показані основні варіанти роторних пазів під обмотку. Усі кромки і кути пазів повинні бути заокруглені для запобігання концентрації механічних напружень у цих місцях Шорсткість поверхні пазів повинна бути не гірше Rz-20.
Дві перші форми пазів (варіанти 1 і II на рис. 17.18) обробляються за один прохід дисковими фрезами, які прорізають прямокутні або напівкруглі пази на всю глибину, а фасонними палевими фрезами виконуються бокові канавки під клини. Фрезерування здійснюється одночасно двох діаметрально розташованих пазів.
Фрезерування пазів за варіантами Ш і IV виконується за декілька проходів. Послідовність обробки таких пазів показана на рис. 17.19.
Свердлування отворів на торцевих поверхнях вал-роторів, бочці ротора і приєднувальному фланці, та нарізання різей у них виконується за допомогою свердлувальних верстатів з горизонтальною віссю шпинделя. Роботи можна виконувати по розмітці або з застосуванням кондукторів.
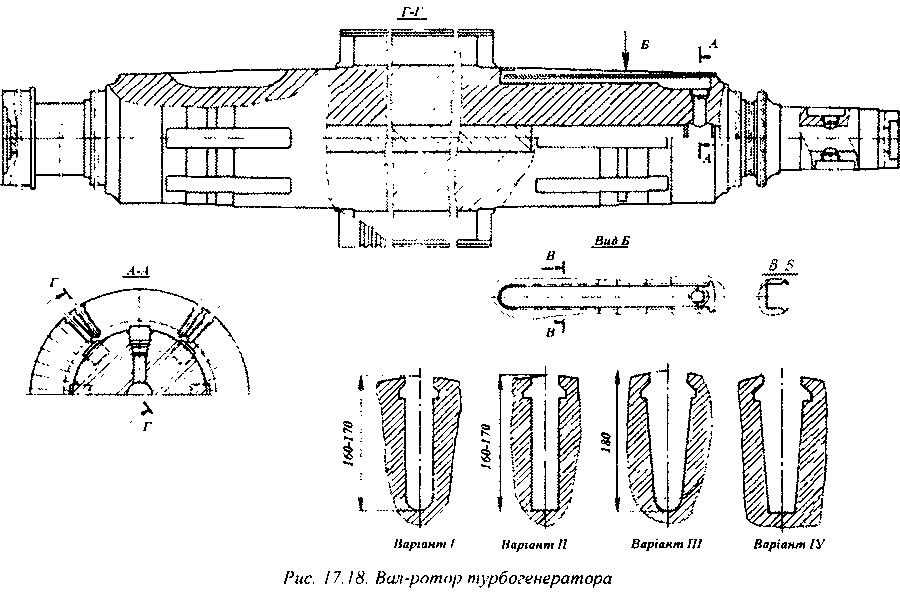
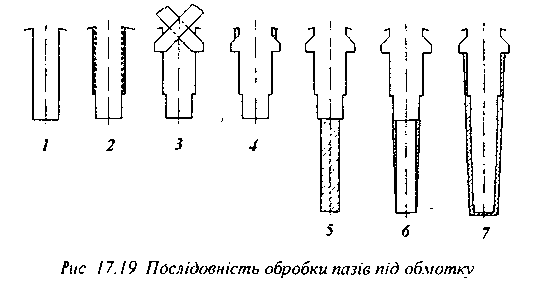
Завершальними операціями обробки вал-роторів є знімання задирок після механічної обробки.