17.1.2. Складання ротора з валом та його кінцева обробка
Як було зазначено вище, місце кінцевої обробки вала в технологічному процесі залежить від його жорсткості, яка визначає спосіб його сполучення з ротором. У сучасній практиці електромашинобудування трапляються такі варіанти сполучення:
• вал гладкий, отвір ротора без попередньої обробки, вал запресовується в холодний ротор;
• вал гладкий, отвір ротора без попередньої обробки, вал запресовується в ротор, який попередньо нагрітий до температури 500 - 550 °С;
• вал гладкий, отвір ротора відкалібровано методом прошивання, вал запресовується в холодний ротор;
• вал гладкий, отвір ротора відкалібровано методом прошивання, вал запресовується в ротор, який попередньо нагрітий до температури 350 °С;
• вал мас рифлену поверхню, отвір ротора відкалібровано методом прошивання, вал запресовується в холодний ротор.
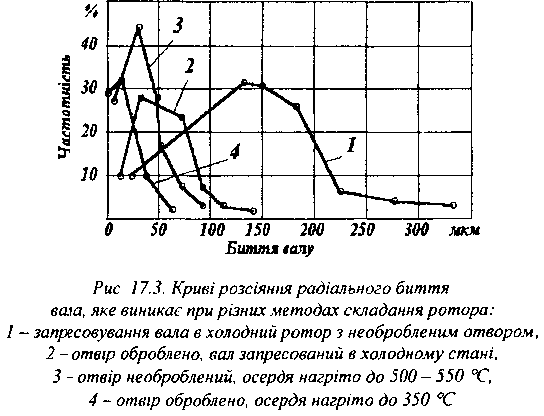
Про вшив методу сполучення можна судити за значенням радіального биття вала (рис. 17.3). З наведеного стає зрозумілим, що найменші биття вала виникають у тих випадках, коли ротор було попередньо нагріто. Крім того, треба брати до уваги, що при нагріванні пакета до температури 420-500 °С в короткозамкнених роторах, виготовлених заливанням алюмінію в осердя, відбувається відрив алюмінієвих стрижнів обмотки від листів заліза, що забезпечує підвищення коефіцієнта корисної дії машини. Однак навіть при використанні найкращого методу складання виникає биття валів, а це вимагає введення кінцевої обробки шийок підшипників і буртиків, на які спираються підшипники. У зв’язку з цим, технологічний процес виготовлення ротора, початок якого було розглянуто в табл. 17.1, треба доповнити операціями, зміст яких наведено в табл. 17.2.
Таблиця 17.2
Виготовлення вала асинхронного двигуна невеликої потужності
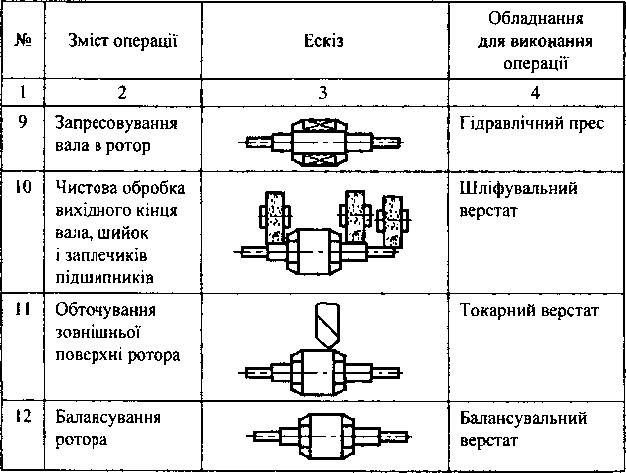
Введення операції обточування зовнішньої поверхні ротора зумовлене необхідністю забезпечення концентричності посадкових поверхонь вала, на які встановлюються підшипники, і зовнішньої поверхні осердя, що особливо важливо для асинхронних і високочастотних машин, які мають малі повітряні проміжки, а радіальне биття осердя при роботі машини не може перевищувати 0,02 - 0,08 мм залежно від потужності машини. Таку обробку потрібно виконувати гострими різцями з твердого сплаву з малими кутами в плані Для запобігання розпушування країв пакетів обробка виконується від країв пакета до середини. У деяких випадках осердя шліфують, але при такій обробці виникають затягування поверхневих шарів сталі, що зумовлює утворення коротхозамкнених контурів, які негативно впливають на показники якості машин.
Для зменшення затягувань застосовують ротаційне обточування, схема якого зображена на рис. 17.4. Операція виконується з використанням ротаційних різців (рис. 17.5). Різальним елементом таких різців використовується кругла пластина з твердого сплаву, яка встановлюється на шпинделі різця.

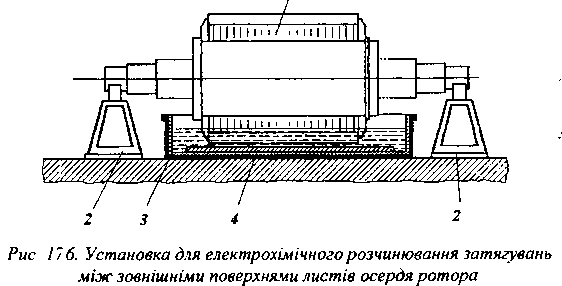
Незважаючи на зазначені заходи зі зменшення затягувань сталі, замикання в поверхневих шарах осердь завжди мають місце. Найбільш надійним способом усунення замикань листів є електрохімічне анодне розчиняння. Схема установки для виконання цієї операції зображена на рис. 17.6. Ротор 1 встановлюється на підставках 2 так, що відстань між поверхнею ротора і мідною шиною 4, вкладеної на дно ванни 3, становить 10-15 мм. Ванна заповнюється 5 % розчином кухарської солі, “плюс” джерела живлення під’єднують до ротора, а “мінус” - до шини. Після завершення електрохімічної обробки ротор промивають гарячою і холодною водою та сушать. На рис. 17.7 показано при 50 кратному збільшенні поверхню осердя до обробки (а) і після обробки (б). На правому рисунку видно, що перемикання між пластинами осердя ліквідовано повністю.
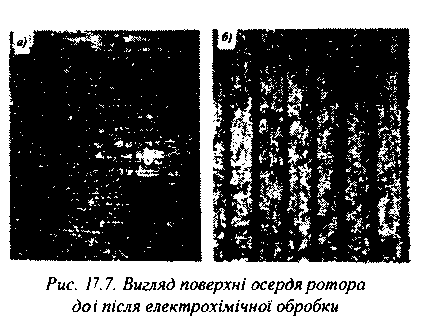